An advanced technology for optimal material control
At 3D Concrete, we use a two-component (2K) concrete 3D printing process that combines mortar with a setting accelerator, injected directly at the print head. This additive technology provides precise control over the rheology of the material. The result: complex and precise forms without formwork—freeform and customized—setting rapidly without deformation.
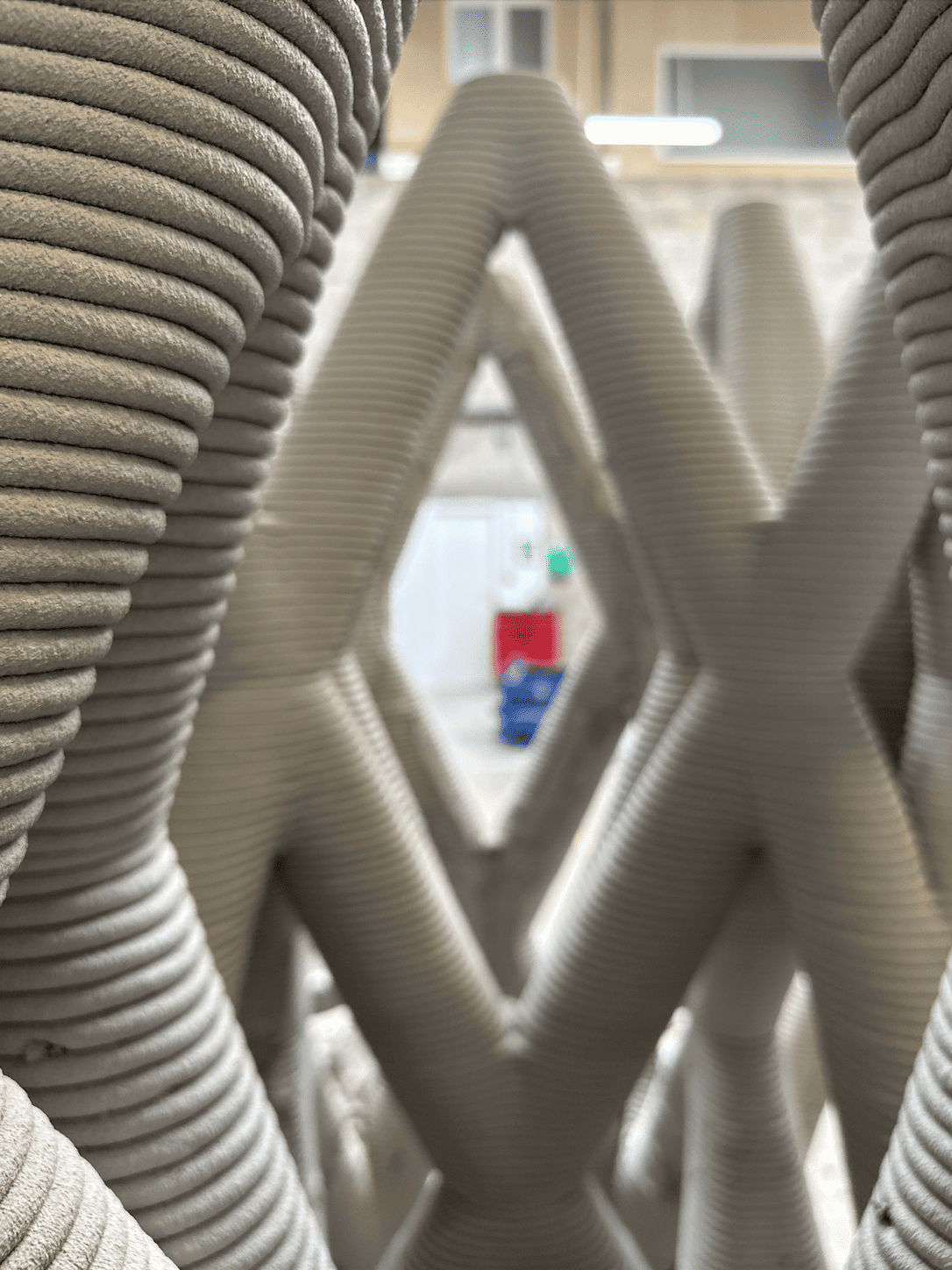
More sustainable formulations
One of the key advantages of this process lies in its compatibility with low-carbon mortars. Thanks to our control over concrete extrusion parameters, we can reduce the amount of water and hydraulic binder required while maintaining excellent mechanical performance. This helps lower the cement content—one of the most CO₂-intensive components—thus significantly reducing the environmental impact of our manufacturing.
Concrete benefits at every stage
Concrete 3D printing offers several practical advantages on construction sites:
– fast execution, minimizing on-site intervention time;
– ability to quickly produce customized elements, even in emergency situations (replacing a part, last-minute adaptations, etc.);
– notable reduction in material used, as parts are often hollow or optimized;
– elimination of traditional formwork or molding stages;
– a more efficient production chain, with reduced costs and a smaller carbon footprint throughout the cycle.
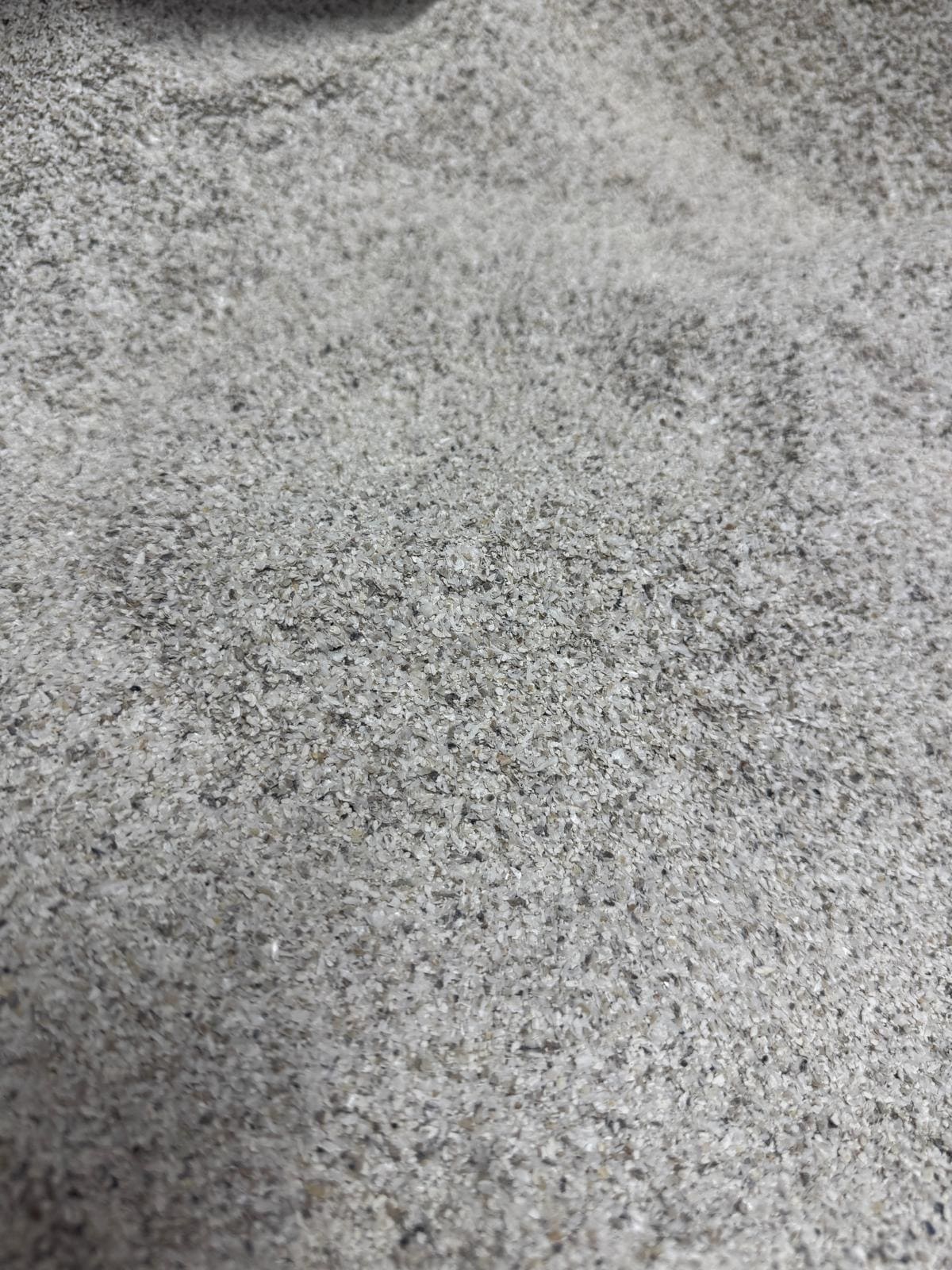
A technology adaptable to other materials
Although our expertise is focused on concrete, our printing system is also compatible with other materials such as geopolymers, plaster, or custom-developed formulations. This flexibility opens the door to various applications, from urban development to design and artistic experimentation.
A concrete example of circular innovation
As part of a collaboration with the company LineUp Ocean, we developed the very first printed mortar incorporating recycled oyster shells. This project perfectly illustrates our commitment to exploring more local and circular alternatives by turning waste into valuable construction resources. This ability to adapt our formulas strengthens our innovative approach to bespoke 3D concrete printing.
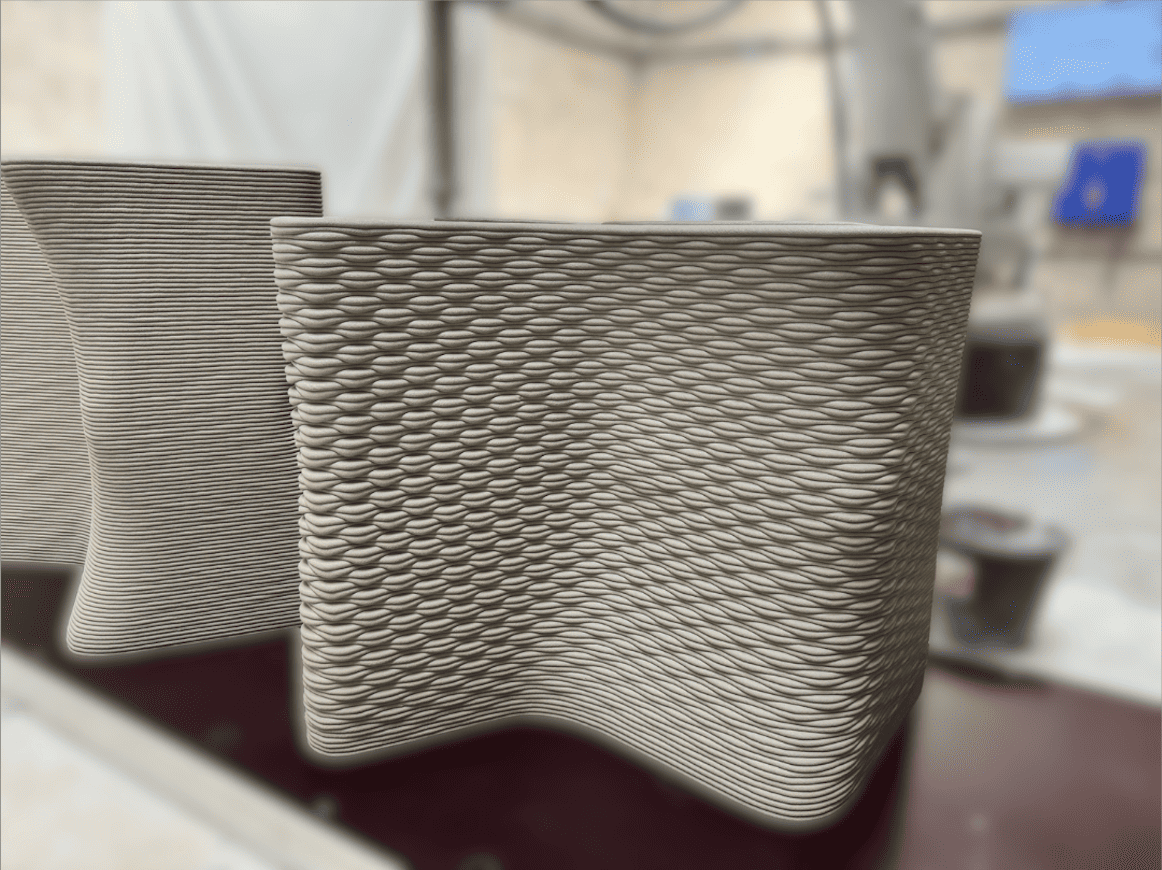
In conclusion
Our 2K system allows us to push the boundaries of what’s possible with concrete 3D printing. By combining technical expertise, material flexibility, and environmental ambition, we are developing a manufacturing method that meets industry demands while anticipating the challenges of tomorrow.
<img src="https://3dconcrete.fr/actualités/https://3dconcrete.fr/3d-admin/actualites/articles/100/edition/2Kconcretetechnology.jpg" alt="3K 3D concrete printing technology by 3D Concrete, Perpignan, Pyrénées-Orientales, Occitanie">